How to get started with Quality Control?
- May 3, 2022
- Posted by: Felicia
- Categories: Advices, Blog, English, Food Safety
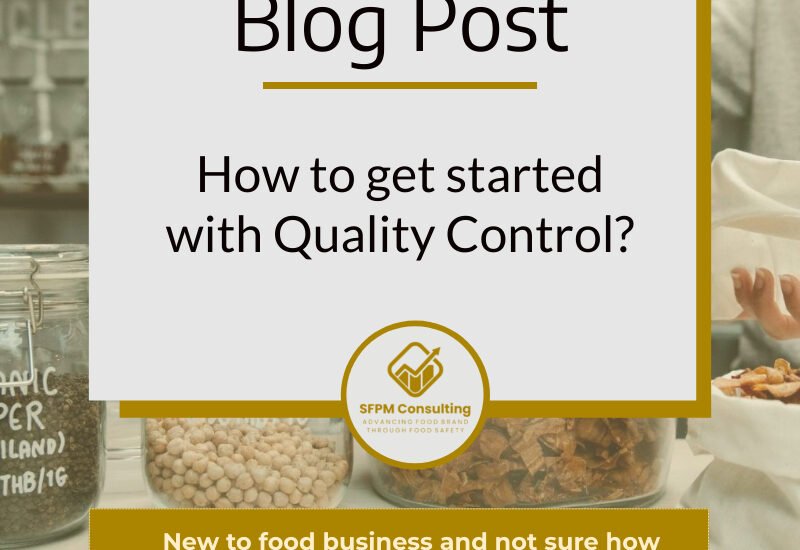
Quality control is a critical process in any manufacturing or production operation. It ensures that products meet the required specifications and are fit for purpose. In this blog post, we will look at how to get started with quality control in your business.
1. What is quality control?
2. The benefits of quality control
3. How to get started with quality control
What is Quality Control?
Quality control is an important part of any manufacturing or production process. It ensures that products meet the required standards and are free from defects. In order to get started with quality control, you first need to understand what it is and why it’s important. You also need to develop a plan for implementing and maintaining quality control in your business. There are many resources available online and offline that can help you get started with quality control.
Quality control is the process of ensuring that products meet the required standards and are free from defects. It involves inspecting products at various stages of production to ensure that they meet the required specifications. Quality control also includes testing products to ensure that they are fit for purpose.
The benefits of quality control
Quality control can have many benefits for your business, including:
-Improved product quality:
By inspecting and testing products at various stages of production, you can identify and fix problems before they cause defects in finished goods. This can improve the overall quality of your products.
-Reduced costs
By identifying and fixing problems early in the production process, you can avoid the costs associated with reworking or scrapping defective products. This can save your business money in the long run.
-Increased customer satisfaction
By providing customers with high-quality products, you can increase customer satisfaction and loyalty. This can lead to repeat business and increased sales.
Implementing Quality Control System
Quality Control is the process of ensuring that products and services meet or exceed customer expectations. It can be applied to anything from manufacturing a product to providing a service.
In order to ensure quality, most organizations have some type of system in place. The most common types of Quality Control systems are:
– Statistical Process Control (SPC)
– Total Quality Management System
– Lean Manufacturing
Each system has its own benefits and drawbacks, so it’s important to choose the one that will work best for your organization.
Statistical Process Control (SPC)
One of the most important aspects of quality control is ensuring that your manufacturing or production process is stable and consistent. This means that you need to be able to track the output of your process over time and identify any changes in the output that could indicate a problem. Statistical Process Control (SPC) is one tool that can help you do this.
With SPC, you collect data on the output of your process over time, and then use statistical methods to analyze that data. This allows you to identify any patterns or trends in the data, which can help you determine whether your process is stable or not. If there are any sudden changes in the data, it could indicate a problem with the process.
3) Taking corrective action: When performance falls short of the standard, corrective action is taken to bring it back into compliance. This may involve changing processes, retraining employees, or redesigning products/services.
4) Continuous improvement: The goal of QC is not just to achieve compliance but also to improve constantly so that products and services
Total Quality Management System (TQM)
TQM is a management approach that seeks to improve the quality of products and services by using a systematic process of continuous improvement. The goal of TQM is to identify and eliminate sources of errors and waste in order to improve the overall quality of the product or service.
TQM tools can also be used to monitor progress towards goals and objectives, as process mapping to document and understand their current processes, identify problems and inefficiencies, and develop solutions or improvements.
– Lean Manufacturing
Lean manufacturing is a production methodology that emphasizes the reduction of waste in all areas of the production process. The goal of lean manufacturing is to produce high-quality products with minimal waste.
Lean manufacturing tools and techniques can be used to streamline processes, reduce costs, and improve quality. Some common lean tools include value stream mapping, 5S, and Kanban.
What is a Quality Management System?
A quality management system (QMS) is a collection of business processes and procedures that together ensure the quality of products or services. It helps an organization to meet customer requirements, as well as statutory and regulatory requirements.
A QMS can be used in any type of organization, from manufacturing and service companies to government agencies and non-profit organizations. The most common elements of a QMS are described below:
1. Customer focus: A QMS must be focused on the needs of customers, both internal and external. This means understanding what customers want/need and making sure those needs are met throughout the entire product or service life cycle.
2. Process approach: All activities within an organization must be structured so that they can be consistently repeated to achieve desired results. This includes defining, measuring, controlling, improving, and verifying all steps in the process so that outputs are consistent with customer requirements.
3 . System approach: A QMS is not just a collection of isolated activities; it should be seen as an integrated system that works together to achieve desired outcomes. This means all aspects of the organization – from production to marketing – must be aligned with the QMS goals and objectives
Steps for Implementing Food Quality Control System
If you’re interested in implementing a food quality control system in your business, there are a few things you need to do:
1. Educate yourself about quality control.
There are many resources available online and offline that can help you learn about quality control. You can find books, articles, and websites that provide information on the basics of quality control.
2. Develop a plan
Once you have a good understanding of quality control, you need to develop a plan for implementing it in your business. This should include setting up procedures and processes for inspecting and testing products. It should also involve training employees on how to carry out these procedures correctly.
3. Implement your plan
Once you have developed a plan, you need to implement it in your business. This may involve making some changes to your production process or investing in new equipment.
4. Monitor and review
Once you have implemented quality control in your business, you need to monitor and review it regularly to ensure that it is effective. You should also make sure that employees are following the procedures correctly.
The Take-Away
Implementing a QC system can be a daunting task, but it’s important to remember that quality control is an ongoing process. It’s not something you do once and then forgets about; it should be an ongoing task. Quality control is a critical process in any manufacturing or production operation.
In order to get started with quality control, it is important to first understand what it is and what its purpose is. Quality control is a process that helps ensure the quality of a product or service by identifying and addressing any issues that may affect it. This can be done at various stages of production, from design and development to delivery and post-sale support.
There are several steps you can take to get started with quality control in your business. The first step is to create a plan outlining how you will achieve quality goals. Next, establish standards for measuring quality, and make sure all employees are aware.
Thank you for reading our guide on quality control. We hope that this information has been helpful and informative. If you have any questions, please do not hesitate to contact us.